Analisi sui nuovi motori a 2T.
Come
sappiamo il 2007 è l'anno in cui le case motoristiche mondiali
hanno cessato la produzione dei motori 2T a carburatore.
Oggi la produzione mondiale di motori vede lo strapotere dei motori
a 4 T, in cui i giapponesi sono i veri Leader di mercato e solo recentemente
le case motoristiche americane stanno cercando di colmare questo gap
tecnologico.
Nel frattempo uno sparuto gruppo di costruttori ha investito nello sviluppo
di motori a 2T di nuova concezione (2T ad iniezione diretta), che sono
in grado di soddisfare i nuovi requisisti ambientali che hanno decretato
la morte del motore a 2 T tradizionale.
Attraverso questa analisi vedremo di comprendere perché i 2T
di nuova generazione potrebbero avere ancora molto da dire in campo
nautico e cercheremo di analizzare tecnicamente le tipologie sviluppate
dai vari costruttori per lo sviluppo dei nuovi motori a 2T ad iniezione
diretta.
Problematiche
dei motori a 2T
Ricordiamo
che il consumo specifico è un parametro importantissimo per un
motore in quanto esso esprime la potenza sviluppata nei termini della
quantità di combustibile spesa per ottenerla ed è utile
per stimare i consumi.
Essa generalmente ha i seguenti valori indicativi:
motori 4T iniezione diretta: 185 gr/CV/h
motori Diesel ad iniezione indiretta: 170 gr/CV/h
motori Diesel ad iniezione diretta: 150 gr/CV/h
motori 2T a carburatori: 320 gr/CV/h.
Per avere i consumi specifici in litri/h dobbiamo ricordare che un litro
di carburante ha un peso specifico 800 gr/litro pertanto se durante
la navigazione il motore eroga 60CV, ecco che con un 2T tradizionale
consumiamo 24 litri/h, mentre con un motore 4T ne consumiamo circa 14
litri/h.
Dobbiamo
ora sfatare un mito, in quanto molti non sanno che i motori a 2T hanno
un'economia di consumi migliore rispetto ad un 4T se non esistesse il
problema della perdita di combustibile allo scarico.
Il grosso problema dei consumi in un 2T tradizionale sta proprio nella
perdita di combustibile allo scarico in cui si arriva a perdere fino
anche il 70% della miscela di carica.
Ecco spiegato perché i 2T tradizionali sono così assetati
rispetto ad una motorizzazione a 4T.
Adesso vediamo di analizzare perché i 2T hanno dei consumi migliori.
Il primo aspetto fondamentale in un 2T è che il valore delle
perdite di pompaggio resta costante al variare del regime di rotazione
(vedi fig.1.1), contrariamente a quanto accade in un 4T in cui esse
aumentano man mano che il regime di rotazione diminuisce.
La
ragione di tutto questo risiede nel fatto che in un motore a 4T le fasi
di ricambio della carica vengono forzate dal moto del pistone, quindi
per ridurre la portata di fluido motore è necessario adottare
una cospicua laminazione in aspirazione alla quale si associa una altrettanto
sensibile dissipazione di energia a carico del propulsore. In un 2T
dato il grande spazio morto tra carter-pompa è sufficiente operare
modeste laminazioni per ottenere forti riduzioni del riempimento e quindi
riduzioni di potenza del motore.
Altro elemento a favore dell'efficienza del motore a 2T è la
minore entità delle perdite per attrito, dovuta sia allo schema
meccanico semplificato che lo caratterizza (assenza di valvole), sia
dal fatto che un ciclo è compiuto in un solo giro; tutto ciò
permette di avere delle pressione medie effettive (pme) più alte
rispetto ad un 4T pertanto a parità di pme si ha un rendimento
maggiore senza poi considerare la presenza dell'apparato di distribuzione
e della pompa dell'olio. Ricordiamo che a parità di cilindrata,
a prescindere dal tipo di motorizzazione, avere una pme alta significa
avere anche una coppia maggiore infatti abbiamo:
C= K*V*pme/125.6
Con K= 1 per un motore a 4T, 2 per un motore a 2T
V= cilindrata espressa in cm3
pme = pressione media effettiva espressa in bar
C= coppia motrice in Nm (se vogliamo i Kgm dobbiamo dividere il valore
ottenuto per 9.81)
I 2
T tradizionali presentano però due grandi problemi:
1) elevate emissioni di incombusti (HC)
2) cattive combustioni.
Questi
problemi sono legati al peculiare processo di sostituzione della carica,
che implica il cortocircuito allo scarico di parte della carica fresca
immessa nel cilindro, la fuoriuscita di questa per effetto del movimento
del pistone ed infine una notevole permanenza dei gas combusti residui
all'interno del cilindro.
Iniezione
diretta e stratificazione della carica sui motori a 2T.
Per rispettare
le nuove normative ambientali (CARB2008, EPA, EURO ecc.) un motore a
2T deve ridurre le emissioni di idrocarburi combusti (HC) e limitare
i problemi delle cattive combustioni senza pregiudicare l'alta potenza
specifica del motore.
Per minimizzare i livelli di HC nella maggior parte dei regimi e dei
carichi possibili è necessario che durante il lavaggio non vengano
perse neanche piccole quantità di combustibile, poiché
queste incrementerebbero in maniera drastica le emissioni.
Per questi motivi si comprende come una efficace riduzione dei consumi
e delle emissioni in un motore 2T debba essere attuata agendo sia sulla
perdita di combustibile, conseguente al processo di lavaggio, sia sul
miglioramento della combustione ai bassi carichi.
Il problema delle perdite di combustibile durante il processo di sostituzione
della carica può essere risolto in modo radicale facendo si che
il carburante non venga coinvolto nel processo di lavaggio. Il combustibile
deve pervenire all'interno del cilindro in modo indipendente dall'aria
e solo dopo che la luce di scarico sia stata chiusa; in questo modo
l'inevitabile cortocircuito interesserà solo l'aria.
La soluzione tecnica naturale è l'iniezione diretta di
combustibile nel cilindro.
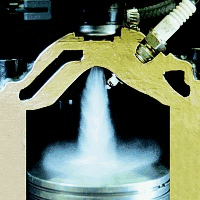
Facile
a dirsi, ma l'iniezione diretta nei motori a 2T risulta più difficile
rispetto a un 4T a causa dei ridotti tempi a disposizione e per fare
un esempio un motore a 2T funzionante a 6000 g/min il tempo a disposizione
per l'iniezione, l'evaporazione ed il mescolamento (eventi non sovrapponibili)
è di circa 2.5 millisecondi.
Il vantaggio dell'iniezione diretta risiede nella possibilità
di aumentare il rapporto di compressione, questo perché l'eventualità
della detonazione risulta più remota dato che il combustibile
introdotto direttamente nella camera di combustione evapora e sottrae
calore alla massa d'aria presente nel cilindro.
L'altro obiettivo da perseguire, ossia il miglioramento della combustione
ai carichi parziali, è quello della stratificazione della carica.
Per stratificazione della carica intendiamo, nel caso dei motori ad
iniezione diretta dopo aver effettuato un abbondante lavaggio atto a
ridurre il più possibile la presenza dei gas combusti nella camera
di combustione, una realizzazione di miscela aria-combustibile stechiometrica
(14.7 parti di aria ed 1 di benzina) solo in prossimità della
candela mentre nel resto della camera di combustione sia avrà
una miscela povera o addirittura solo aria (si hanno mediamente valori
da 30 a 50 parti di aria ed 1 di benzina).
In questo modo viene facilitato l'innesco della combustione oltre che
il suo progredire fino al coinvolgimento di tutto il combustibile presente
nella camera di combustione.
La strategia per ottenere la stratificazione è quello di operare
una iniezione ritardata (late injection), quindi i tempi sono ancora
più ristretti di quelli indicati in precedenza anche se la stratificazione
si effettua a regimi medio bassi. Occorre inoltre avere una pressione
di iniezione elevata per l'ottenimento di un grado di microomogeneità
accettabile dato che si inietta in un ambiente a pressione maggiori
di 5 bar.
Il bassissimo tempo a disposizione per la combustione costituisce il
maggiore vincolo, poiché se al momento dell'innesco sono presenti
ancora parti di carburante non completamente evaporato o miscelato all'aria,
questo brucia più lentamente dando origine ad una notevole emissione
di particolato.
Un ulteriore vantaggio della stratificazione della carica è la
possibilità di alimentare il motore con una miscela complessivamente
povera ottenendo così delle temperature di combustione minori
e quindi meno produzione di NOx.
Sviluppi
dell'iniezione diretta nei motori a 2T
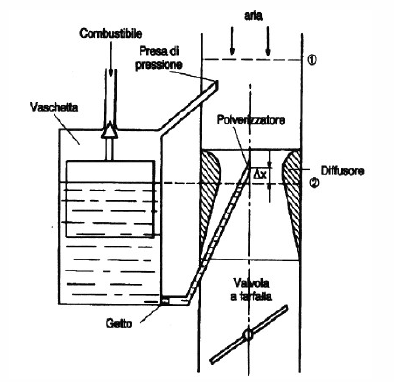
Il carburatore
ha rappresentato fino ad oggi la soluzione più economica per
il 2T, il principio di funzionamento, come noto si basa sul cosiddetto
effetto Venturi, consistente in una trasformazione da energia di pressione
in energia cinetica indotta da un opportuno restringimento della sezione
del condotto (figura 1.2).
Fig.1.2 carburatore elementare
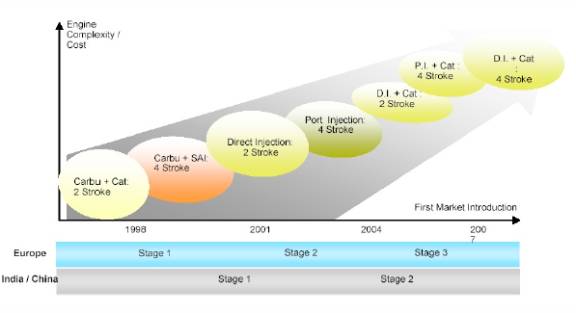
Il ricorso
ai sistemi di iniezione è stato quindi una inevitabile necessità
in campo automobilistico/ motociclistico a causa di pressioni legislative
di numerosi governi (Stati Uniti, Comunità Europea, Giappone).
In questi anni si è avuto un fortissimo impulso nella ricerca
di sistemi innovativi di formazione della miscela e la conseguenza di
ciò è stato il raggiungimento di risultati che fino a
poco tempo fa potevano sembrare impensabili (fig 1.3)
Fig. 1.3 progresso tecnologico subito
Come ricordato
in precedenza, per l'applicazione di sistemi ad iniezione diretta, nel
caso di un motore a 2T si incontrano, a parità di condizioni,
maggiori difficoltà perché si deve operare con una frequenza
di iniezione doppia rispetto ad un motore a 4T. In figura 1.4 è
rappresentato uno schema classico di motore a carburatore, mentre in
fig.1.5 è rappresentato uno schema di motore ad iniezione diretta.
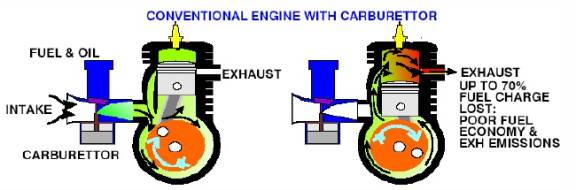
Fig. 1.4 motore convenzionale con carburatore
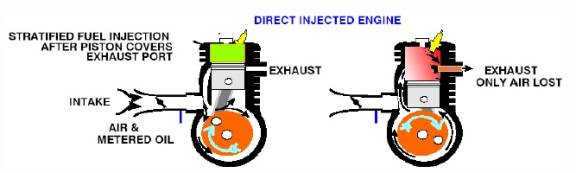
Fig. 1.5 motore 2T ad iniezione diretta
Un grande
aiuto alla diffusione dei sistemi ad iniezione diretta è stato
dato da sofisticati sistemi di controllo elettronico che permettono
di utilizzare circuiti e mappature di centraline molto complesse in
grado di eseguire in modo ottimale le mutevoli esigenze del motore.
Per quanto riguarda il problema del ridotto tempo a disposizione per
preparare una miscela dalle caratteristiche adeguate, la soluzione viene
fornita da iniettori ad alta pressione in grado di generare uno spray
finemente polverizzato, in modo tale da avere in un intervallo di tempo
ridotto una omogeneizzazione della carica almeno intorno alla candela.
Le caratteristiche dello spray dipendono da numerosi fattori, di cui
i principali sono:
1) caratteristiche geometriche dell'iniettore
2) parametri del sistema di iniezione (pressione)
3) condizioni fluidodinamiche e termodinamiche dell'aria all'interno
della camera di combustione (grado di turbolenza, densità,
ecc.)
4) caratteristiche geometriche della camera di combustione.
Particolare
attenzione deve essere posta all'ultimo fattore, in quanto risulta decisivo
per ottenere la stratificazione a vari regimi di rotazione, inoltre
si deve posizionare l'iniettore in punti strategici nella camera di
combustione.
Qui entrano le esperienze e le ricerche effettuate dai costruttori per
le varie ottimizzazioni ad esempio il sistema GDI Mitsubishi ha adottato
una particolare conformazione del cielo del pistone, il quale diventa
un elemento attivo nella fase di formazione della carica deviando il
flusso di combustibile, proveniente dall'iniettore, verso la candela
in modo da garantire in prossimità di questa un sufficiente apporto
di benzina (fig. 1.6).
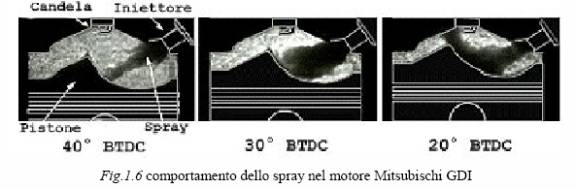
Questo esempio anche se si riferisce ad un motore a 4T mette in evidenza
l'importanza che può assumere la geometria della camera di combustione,
non solo per impartire la necessaria turbolenza al flusso d'aria in
ingresso ma anche come mezzo determinante per ottenere una carica stratificata.
Sistemi
ad iniezione diretta applicati ai 2T ad accensione comandata.
Numerose
soluzioni sono state proposte finora da diversi costruttori ed in ogni
caso possiamo distinguere tra i seguenti sistemi di base:
a) sistemi
air-assisted
Si ha una
iniezione diretta di miscela aria/combustibile molto ricca, poiché
si è visto che iniettando una emulsione con queste caratteristiche
si migliora la polverizzazione del combustibile aumentando la velocità
di polverizzazione, con minori tempi di deposito di combustibile in
corrispondenza dell'apertura dell'iniettore. Questo miglioramento comporta
in realtà una maggiore complicazione del sistema e sopratutto
un controllo peggiore sulla quantità di benzina iniettata. I
sistemi proposti da Piaggio, IAPAC, Orbital, hanno il vantaggio di una
elevata velocità del getto (legata all'energia cinetica), ma
vi è una grossa difficoltà nello stratificare poiché
si hanno basse pressioni di iniezione.
b) sistemi single fluid
Praticamente
consiste nella iniezione di solo combustibile, è sicuramente
il modo più naturale e concettualmente più semplice per
operare una iniezione, ma deve far fronte al limitato tempo a disposizione
per creare la giusta miscelazione tra aria e combustibile. Necessita
di alte pressioni di iniezione e presenta rischi di depositi carboniosi
sulla testa dell'iniettore. Tra i sistemi proposti più interessanti
sono Ficth e Ram Tuned.
Analizziamo ora brevemente i sistemi di iniezione appena menzionati.
1) Piaggio
Fast
Nel sistema Fast (fig. 1.7) la pressione di iniezione pari a 3-4 bar
è generata da un compressore a stantuffo collocato sulla testa
del cilindro ed azionato dall'albero motore tramite cinghia di trasmissione.
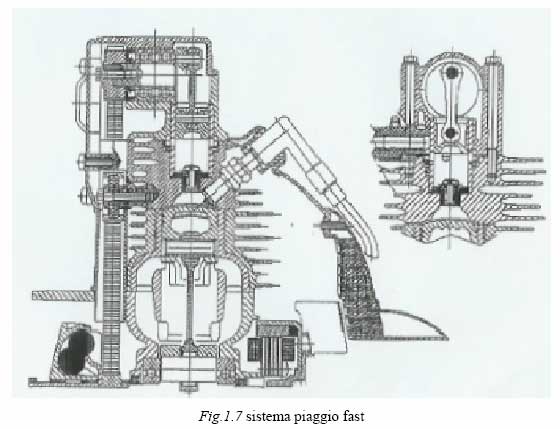
Il combustibile proveniente dal carburatore entra nel compressore dove
si forma una miscela ricca. Il Vantaggio di questa soluzione sta nella
possibilità di far pervenire il combustibile nel cilindro con
un ritardo adeguato a dar luogo alla stratificazione della carica. Infatti
quando la differenza di pressione tra cilindro e cilindretto del compressore
supera 3 bar, una valvola si apre automaticamente determinando il passaggio
della miscela ricca dal compressore alla camera. Purtroppo questo motore
non è mai stato sviluppato per poter realizzare la stratificazione
bensì per il funzionamento in carica omogenea con gli inconvenienti
di cattive combustioni ai bassi carichi, tipiche dei 2T tradizionali.
Inoltre la soluzione Piaggio Fast è costruttivamente complessa
e costosa.
2) Motore
a carica stratificata dell 'Institut Francais du Pétrole (IAPAC)
L'IFP ha sviluppato un sistema che sfrutta l'aria compressa dal carter-pompa
per assistere l'iniezione del combustibile. Tale sistema denominato
IAPAC ( dal francese Injection Assistee Par Air Comprimè) è
schematizzato in fig. 1.8.
Da questo si può comprendere il principio di funzionamento: il
carter riempie un serbatoio di accumulo con aria compressa grazie ad
una valvola a lamelle; da qui l'aria fluisce nel cilindro attraverso
una valvola a fungo.
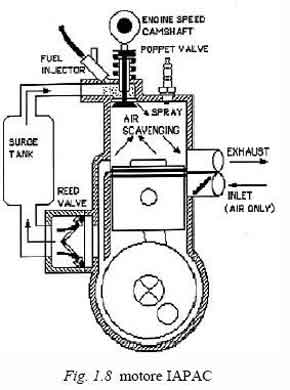
Un iniettore a bassa pressione inietta una data quantità di combustibile,
che va a depositarsi sul fungo della valvola; in questo modo il combustibile
ha un certo tempo di residenza che permette una parziale evaporazione
prima dell'apertura della valvola e quindi dell'iniezione vera e propria
nel cilindro. La qualità del getto aria-benzina è ulteriormente
migliorata dalla forma a tubo di Venturi della sede valvola. La restante
parte di benzina non evaporata avrà tutto il tempo necessario
per miscelarsi con l'aria pompata attraverso le classiche luci di lavaggio.
Da notare l'estrema importanza della posizione valvola-iniettore: sufficientemente
lontana dalla luce di scarico, per ridurre al massimo i pericoli di
cortocircuito e strategicamente collocata in modo tale da facilitare,
con l'interazione dei flussi interni al cilindro, la formazione di una
miscela stratificata a partire dalla posizione della candela. I risultati
al banco di prova ottenuti con un motore di 250 cm3 sono stati una potenza
massima raggiunta di 15 CV a 4500 giri/min, quindi si ricava una potenza
specifica di 60 CV/litro con consumi specifici pari a 185 gr/CV/h.
Gli svantaggi di questo sistema di iniezione sono:
a) motore costruttivamente complicato e quindi costoso
b) non si ha la possibilità di ottenere una buona stratificazione,
poiché si deve iniettare piuttosto in anticipo rispetto al punto
morto superiore perché all'interno del serbatoio di accumulo
non si raggiungono pressioni elevate.
In campo nautico il motore IFP è stato adottato dal costruttore
SELVA.
3) ORBITAL
Il cuore di questo sistema è un iniettore comandato da un solenoide
che inietta una miscela aria-combustibile finemente polverizzata direttamente
nella camera di combustione (fig. 1.9 illustra il sistema di iniezione).
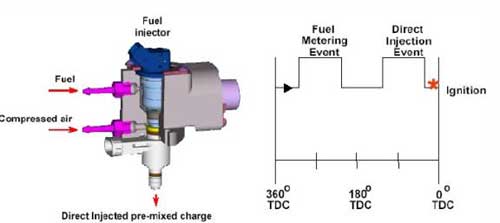
Fig. 1.9 Gruppo di iniezione ORBITAL e sequenza di iniezione
L'iniettore
del combustibile prima invia una quantità controllata di combustibile
nella camera ad aria nella quale si raggiunge una pressione di 6 bar
in corrispondenza dell'iniettore ad aria, quest'ultimo inietta la miscela
di aria e benzina sotto forma di una nuvola finemente polverizzata.
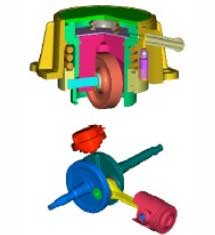
Le piccole
dimensioni delle particelle che si possono ottenere con questo sistema
a bassa pressione permettono una evaporazione molto veloce del combustibile,
minimizzando il tempo per la preparazione della miscela all'interno
del cilindro. Questo sistema, in combinazione con un'adeguata forma
della testata e della cielo del pistone, entro certi limiti permette
il processo di stratificazione della carica. L'aria compressa richiesta
per il processo di iniezione è fornita generalmente da un piccolo
compressore a stantuffo azionato da una camma posta sull'albero motore
come mostrato in fig. 1.10
Fig.
1.10 Compressore ORBITAL
Il combustibile è invece fornito da una pompa convenzionale operante
ad una pressione compresa tra 6.2 e 7.2 bar (fig. 1.11).
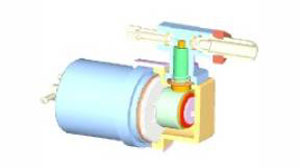
Fig. 1.11 pompa della benzina del sistema ORBITAL
I risultati
di questo sistema sono notevoli: bassi consumi specifici (si può
raggiungere un'economia fino al 20% rispetto ai 2T convenzionali con
valori che si aggirano sui 220-260 gr/CV/h), riduzioni drastiche di
HC e CO. L'olio viene gestito mediante un ulteriore sistema di iniezione
che provvede a lubrificare i punti critici del motore ottenendo fumosità
zero e candele sempre pulite.
Gli inconvenienti di questo sistema sono molteplici tra i quali si ricorda:
a) la pressione di iniezione si aggira intorno a 6 bar, quindi non è
possibile ritardare molto la fase di iniezione, poiché la pressione
all'interno del cilindro sale bruscamente dopo la chiusura dello scarico.
Del resto innalzare la pressione di iniezione comporterebbe uno spreco
di lavoro eccessivo ai bassi carichi.
b) L'iniettore tende a sporcarsi poiché, per mantenere un minimo
di stratificazione e non potendo iniettare in ritardo, si deve accendere
quando l'iniettore è ancora aperto, questo implica che parte
dei gas combusti entrano all'interno dell'iniettore stesso, formando
depositi carboniosi; inoltre l'accensione anticipata pregiudica il rendimento
del motore.
c) Il sistema risulta complesso e costoso.
Questo sistema è stato adottato da Aprilia (DI Tech) e successivamente
da Piaggio (Pure Jet) e in campo nautico da MERCURY con i suoi Optimax
e da TOHATSU con i suoi TLDI.
4) Sistema
di iniezione FICHT
Questo dispositivo inietta all'interno della camera di combustione solo
combustibile. La modalità con cui viene fornita pressione al
fluido è abbastanza semplice ed intuitiva: tenendo presente le
due figure 1.12 ed 1.13
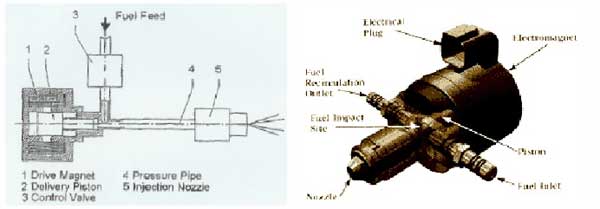
Fig. 1.12 schema dell'iniettore FICHT Fig.1.13 vista dell'iniettore
FICHT
il combustibile
viene dapprima pompato all'interno del piccolo cilindro dell'iniettore
mentre lo stantuffo pompa si porta al punto morto per poi essere accelerato
dal solenoide sempre mantenendo la valvola 3 aperta. Lo stantuffo nel
suo moto chiude la valvola 3, la pressione del combustibile si innalza
causando l'inizio dell'iniezione. Il sistema ha il pregio di raggiungere
il completamento dell'iniezione in breve tempo, oltre ad avere buone
caratteristiche dello spray, tali da garantire elevata efficienza e
bassi consumi analoghi ad un motore a 4T di pari potenza (si veda anche
la prova comparativa tra johnson 90CV 4T ed E-TEC 90 CV, comparsa sulla
rivista Il Gommone n°227). Complessivamente il sistema risulta composto
da pochi elementi di piccolo ingombro e di forma allungata che si adatta
perfettamente all'alloggiamento in una piccola testata di un motore.
Occorre sottolineare che questo dispositivo ha un principio di funzionamento
simile a quello del sistema Ram Tuned (successivamente descritto), nel
senso che viene sfruttato in entrambi il fenomeno del colpo d'ariete,
ma, mentre nel Ram Tuned è il fluido che accelera per poi arrestarsi
improvvisamente alla chiusura di una valvola, nel sistema Fitch è
un pistone che va ad impattare contro il fluido mandandolo in pressione.
Le caratteristiche di questo sistema di iniezione sono particolarmente
adatte ad un motore a 2T: la curva di pressione e quindi la qualità
dello spray è indipendente dalla quantità iniettata di
combustibile e dalla velocità del motore; essendo molto breve
il picco di pressione (0.2-1.5 millisecondi; 25-65 bar) permette al'iniettore
di aprirsi e chiudersi velocemente, consentendo così una buona
polverizzazione del combustibile. In tali circostanze possono essere
iniettate sia piccole che grandi quantità di combustibile( da
1 a 50 mm3). Il sistema può essere totalmente controllato in
maniera elettronica in quanto è meccanicamente disaccoppiato
dal motore è così possibile operare le correzioni necessarie
ad un buon funzionamento nelle varie condizioni di carico, velocità,
temperatura ecc.; sono possibili velocità di rotazione del motore
molto elevate (maggiori di 10000 giri/min) grazie al breve tempo necessario
all'iniezione e all'inerzia elettro magnetomeccanica relativamente bassa.
Il sistema di lubrificazione è analogo al sistema Orbital.Grazie
alla compattezza dell'iniettore esiste la possibilità di installarlo
anche su piccole cilindrate.
Gli svantaggi principali di questo sistema sono:
a) non linearità del controllo, causata dalla dinamica molto
variabile del sistema.
b) Se la valvola in testa all'iniettore si snerva, la portata varia
in misura notevole
c) L'iniezione non avviene a pressione costante, questo ha come conseguenza
una dispersione del diametro medio delle gocce e quindi una diversa
penetrazione e velocità del getto, il che penalizza la stratificazione
della carica.
Questo sistema è stato adottato da EVINRUDE con i suoi E-TEC.
5) Sistema
di iniezione diretta Ram Tuned
Il principio di funzionamento di questo sistema, nato inizialmente per
i motori Diesel, si basa sul ben noto fenomeno detto comunemente colpo
d'ariete: un generico fluido in movimento e arrestato improvvisamente,
da luogo ad un aumento di pressione. Una analisi teorica del fenomeno
è quanto mai complessa, l'unico modo per analizzare quantitativamente
il colpo d'ariete per poi sfruttarlo in un sistema di iniezione è
la sperimentazione diretta. Lo schema del sistema Ram Tuned è
mostrato in fig.1.14 ed è composto da elementi comuni e facilmente
reperibili sul mercato.
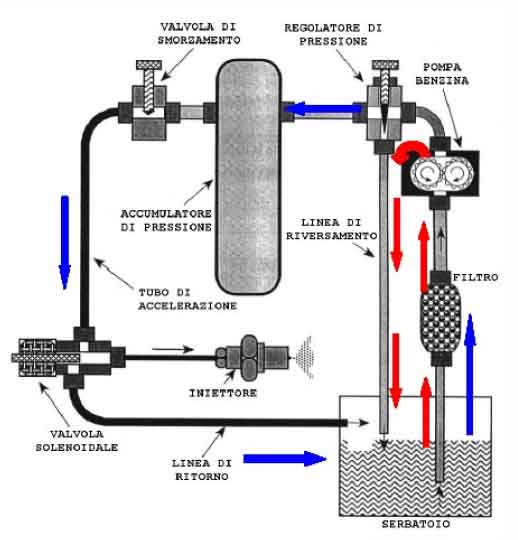
Fig. 1.14 schema del sistema Ram Tuned
Le fasi
in cui si svolge il ciclo di iniezione sono sostanzialmente tre. In
una prima fase, la valvola a solenoide è inizialmente chiusa,
impedendo così il passaggio di combustibile nel circuito secondario
(filtro-pompa-regolatore di pressione- accumulatore di pressione - valvola
di smorzamento- tubo di accelerazione-linea di ritorno, ossia il circuito
segnato in blu nella fig.1.14)
Quindi il fluido passerà soltanto lungo il circuito primario
(filtro-pompa - regolatore di pressione- linea di riversamento, ossia
il circuito segnato in rosso della fig. 1.14), grazie all'azione di
una pompa che fornisce un valore di pressione generalmente fissato tra
i 4 e 6 bar, ritornando direttamente al serbatoio.
La seconda fase prende inizio nel momento in cui viene aperta la valvola
a solenoide grazie al comando generato da una centralina elettronica.
A questo punto il combustibile è libero di muoversi attraverso
il circuito secondario, accelerando fino al momento in cui viene chiusa
di nuovo la valvola solenoide. La terza ed ultima fase inizia, con l'impatto
del fluido in movimento contro la valvola seguito da una crescita immediata
della pressione fino a valori massimi prossimi ai 50-60 bar. Il segnale
di pressione si propaga come un'onda alla velocità del suono
all'interno delle tubazioni (parliamo di 5000 m/sec), raggiungendo in
particolare l'iniettore; la pressione vince la forza di opposizione
dello spillo ed inizia l'iniezione. L'onda generata si propaga anche
in direzione opposta alla corrente fluida, raggiungendo un dispositivo
di smorzamento in grado di assorbire parte dell'energia trasportata.
In tale modo si evita che i picchi di pressione riflessi possano portare
ad aperture indesiderate dell'iniettore. Una volta finito l'effetto
del colpo d'ariete in breve tempo il sistema si ristabilizza ritornando
alle condizioni iniziali. Attraverso prove sperimentali si è
verificato che le caratteristiche dell'onda di pressione sono indipendenti
dalla frequenza di funzionamento in una gamma piuttosto ampia che va
da 1 Hz a 200 Hz (ossia regimi di rotazione da 60 g/min a 12000 g/min).
Il sistema di lubrificazione è analogo a quello descritto nel
sistema Orbital.
Questo sistema ha gli stessi svantaggi del sistema Ficht ma aggravati
dall'alta sensibilità alle eventuali bolle di vapori/aria nei
condotti.
Questo sistema è stato adottato da YAMAHA con i suoi HDPI.
Riflessioni
L'evoluzione
dei sistemi di iniezione e dell'elettronica nella gestione del motore
ha permesso di ridurre drasticamente le emissioni riportandole entro
i valori che richiedono le normative ambientali e come conseguenza abbiamo
sul mercato motori a 2T di nuova generazione con consumi simili a quelli
dei 4T, ma come svantaggio abbiamo perso la semplicità originaria
di un 2T tradizionale in cui si poteva intervenire sui malfunzionamenti
armati di pinza, chiave e cacciavite e ripartire.
Ogni casa costruttrice (Tohatsu, Mercury, Evinrude, Yamaha, Selva) ha
adottato filosofie differenti ed il motore a 2T ad iniezione diretta
perfetto non esiste, sarà il tempo a decretare la tecnologia
vincente tra i nuovi 2T, in funzione dell'affidabilità dei motori
e dell'assistenza della case costruttrici. Possiamo dire che il sistema
di iniezione diretta ha trovato applicazione commerciale nei motori
marini, dimostrando prestazioni interessanti in quanto consumi ed emissioni
sono comparabili con quelli dei motori a 4T.
La scelta di ognuno di noi tra un 4T ed un 2T ad iniezione diretta dovrà
tener conto di vari parametri quali:
1) ore annuali di navigazione, in modo da considerare i costi dei consumi
di olio ( nel caso dei motori ETEC è lo 0.5% ) del 2T rispetto
al cambio dell'olio motore presente nel 4T
2) minori costi e problemi di manutenzione di un 2T di nuova generazione
rispetto ad un 4T (olio motore e filtro da cambiare , cinghia della
distribuzione, ecc.).
3) Pesi ed ingombri rispetto ad un motore 4T di pari potenza
4) Migliore coppia disponibile rispetto ad un 4T.